air compressor manual
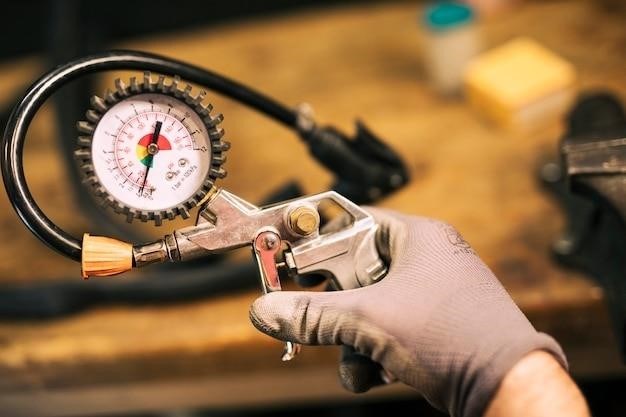
Air Compressor Manual⁚ A Comprehensive Guide
This manual offers a comprehensive guidance to anyone who is looking forward to further explore and get insights in compressed air technology. Whether you are a professional technician, a DIY enthusiast, or simply curious about the workings of air compressors, this manual will provide you with valuable information.
Introduction
Air compressors are powerful and versatile tools that have become essential in various industries and workshops. They work by compressing air, creating a pressurized source of energy that can power a wide range of pneumatic tools and equipment. From inflating tires and spraying paint to operating jackhammers and powering airbrushes, air compressors are indispensable for a multitude of tasks.
This comprehensive manual serves as a guide to understanding the intricacies of air compressors, covering various aspects from their different types and applications to their safety protocols, maintenance procedures, and troubleshooting techniques. Whether you are a professional mechanic, a DIY enthusiast, or simply seeking to expand your knowledge on these powerful machines, this manual will provide you with the necessary information to operate, maintain, and troubleshoot air compressors effectively.
Types of Air Compressors
Air compressors are broadly classified into three primary types⁚ reciprocating, rotary screw, and centrifugal. Each type operates on a distinct principle and is best suited for specific applications.
Reciprocating compressors are the most common type, known for their simplicity and affordability. They utilize a piston moving within a cylinder to compress air. Reciprocating compressors are often found in smaller workshops and garages, suitable for tasks like inflating tires and powering small air tools. Rotary screw compressors, on the other hand, employ two intermeshing screws to compress air. They are known for their high efficiency and continuous operation, making them ideal for industrial applications requiring a consistent supply of compressed air.
Centrifugal compressors, also known as turbo compressors, use a rotating impeller to compress air; These compressors are highly efficient and capable of generating high volumes of compressed air at high pressures, making them suitable for large-scale industrial processes. The choice of air compressor type depends on factors such as the required pressure, air volume, and the specific application.
Applications of Air Compressors
Air compressors are versatile machines with a wide range of applications across various industries. Their ability to provide compressed air makes them indispensable for powering pneumatic tools and equipment, which are essential for diverse tasks. In construction, air compressors are used to operate jackhammers, nail guns, spray guns, and other tools necessary for building projects. They are also vital in manufacturing, powering pneumatic drills, grinders, sandblasters, and other tools for production processes.
Beyond industrial applications, air compressors find use in automotive repair shops for inflating tires, powering air wrenches, and cleaning parts. In healthcare settings, they are employed for medical equipment like nebulizers and dental drills; Additionally, air compressors are used in recreational activities such as scuba diving and paintball, providing the necessary compressed air for equipment. Their versatility makes them a valuable tool in various sectors, contributing to productivity and efficiency.
Air Compressor Safety
Operating an air compressor requires a strong emphasis on safety to prevent accidents and injuries. Before using any air compressor, it is crucial to read and understand the manufacturer’s instructions and warnings provided in the user manual. Always disconnect the compressor from the power source and release the compressed air from the air tank before inspecting, maintaining, cleaning, replacing, or performing any repairs. Never attempt to operate the compressor if you are unsure of any procedures or if the equipment appears damaged or malfunctioning.
Ensure that the compressor is properly grounded and connected to a suitable power source. When using the compressor, wear appropriate safety gear such as eye protection, hearing protection, and sturdy footwear. Be aware of the potential hazards associated with high-pressure air, such as flying debris or projectiles. Always maintain a safe distance from the compressor’s exhaust and discharge points. Regularly inspect the compressor for leaks, wear, and damage, and address any issues promptly. By following these safety precautions, you can minimize the risk of accidents and ensure a safe operating environment.
Air Compressor Maintenance
Regular maintenance is essential for ensuring the longevity and optimal performance of your air compressor. A well-maintained compressor operates efficiently, reduces the risk of breakdowns, and extends its lifespan. Start by adhering to the manufacturer’s recommended maintenance schedule, which typically outlines specific tasks and intervals. Regularly inspect the air compressor for signs of wear, leaks, or damage. Pay close attention to the air filter, which should be cleaned or replaced as needed to prevent dust and debris from entering the compressor.
Check the oil level and quality, topping it off or changing it as recommended. Inspect the belts and hoses for cracks, fraying, or leaks, and replace them if necessary. Ensure the air tank drain valve is functioning properly and is drained regularly to remove moisture and contaminants. Keep the compressor’s exterior clean and free of debris, and lubricate moving parts as instructed. By following these maintenance procedures, you can ensure your air compressor operates reliably and efficiently for years to come.
Troubleshooting Common Air Compressor Issues
While air compressors are generally reliable machines, they can experience occasional issues. Here are some common problems and how to troubleshoot them⁚ If your compressor fails to start, check the power supply and make sure the circuit breaker is not tripped. Inspect the motor for signs of damage or overheating. Ensure the air tank pressure switch is properly set and functioning. If the compressor runs but produces little or no air pressure, check for leaks in the hoses, fittings, or air tank. Inspect the air filter for clogging, as this can restrict airflow.
If the compressor runs continuously without building pressure, the pressure switch may be malfunctioning or the air tank pressure relief valve could be stuck open. Excessive noise or vibration may indicate a problem with the motor, bearings, or connecting rods. Always consult the manufacturer’s manual for specific troubleshooting steps and safety precautions. If the issue persists, it’s advisable to contact a qualified technician for assistance.
Air Compressor Accessories
Air compressors are versatile tools that can be enhanced with a range of accessories to expand their functionality and efficiency. These accessories can be tailored to specific applications and user needs. Commonly used accessories include air hoses, which connect the compressor to pneumatic tools, and quick-connect fittings that facilitate easy tool attachment and detachment. Air filters, which trap dust and debris, protect the compressor and tools from contamination. Pressure regulators allow you to adjust the air pressure output, ensuring optimal performance for different tasks.
Air compressor accessories also include air tanks, which store compressed air and provide a buffer for consistent pressure. Air dryers remove moisture from the compressed air, preventing condensation and corrosion in tools and equipment. Lubricators dispense oil into the compressed air stream to reduce friction and wear in pneumatic tools. These accessories can significantly enhance the performance and longevity of your air compressor, making it a more versatile and efficient tool for various applications.
Environmental Considerations
Air compressors, while powerful and versatile, can have environmental implications. The primary concern is air pollution, as compressors release exhaust gases during operation. These gases can contribute to smog and respiratory problems, particularly in urban areas. Additionally, some compressors use refrigerants, which can contribute to ozone depletion if they leak into the atmosphere. It’s important to choose compressors that meet environmental standards and use energy-efficient models to minimize emissions. Regular maintenance and proper disposal of used components also play a crucial role in reducing environmental impact.
Consider investing in compressors with low noise levels, as excessive noise pollution can be detrimental to nearby communities. Properly dispose of oil and filters to prevent contamination of soil and water sources. By being mindful of these environmental considerations, you can utilize air compressors responsibly and minimize their impact on the environment.
Air compressors are indispensable tools in a wide range of applications, from automotive repair to construction projects. Understanding the different types, applications, and safety procedures associated with air compressors is crucial for maximizing their utility and ensuring safe operation. Regular maintenance, proper troubleshooting, and the use of appropriate accessories will extend the life of your compressor and enhance its performance.
Always prioritize safety when working with air compressors, following the guidelines outlined in this manual. By adhering to these recommendations, you can ensure the efficient and safe operation of your air compressor, maximizing its potential and minimizing potential risks; Remember, a well-maintained and properly operated air compressor can be a valuable asset for any individual or business.