taylor ice cream machine manual
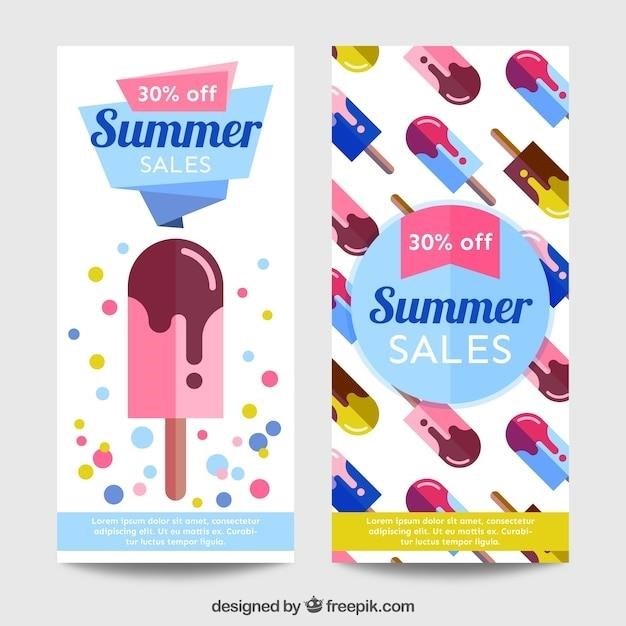
Taylor Ice Cream Machine Manuals
Taylor ice cream machines are a popular choice for businesses that serve soft serve ice cream‚ frozen yogurt‚ and other frozen treats. These machines are known for their reliability and durability‚ but like any piece of equipment‚ they can sometimes require maintenance or repairs. If you own a Taylor ice cream machine‚ it’s essential to have a copy of the operator’s manual readily available. The manual provides detailed instructions on how to operate‚ maintain‚ and troubleshoot your machine. It also contains safety information and warranty details.
Introduction
Taylor ice cream machines are a staple in the food service industry‚ known for their reliable performance and ability to churn out delicious soft serve‚ frozen yogurt‚ and other frozen treats. Whether you’re a seasoned ice cream connoisseur or a curious newcomer to the world of frozen desserts‚ understanding your Taylor ice cream machine is essential for producing top-notch treats and ensuring a smooth operation. This manual serves as your comprehensive guide to navigating the intricacies of your Taylor ice cream machine‚ providing detailed information on its operation‚ maintenance‚ troubleshooting‚ and safety procedures. From priming the freezing cylinder to understanding potential beeping alerts‚ this manual equips you with the knowledge to confidently operate and maintain your Taylor ice cream machine‚ guaranteeing a delightful experience for both you and your customers.
Popular Taylor Ice Cream Machine Models
Taylor offers a diverse range of ice cream machines‚ catering to various needs and production volumes. Popular models include the C723‚ C713‚ C712‚ C707‚ 8756‚ 794‚ 754‚ 340‚ 751‚ 702‚ 490‚ 430‚ 390‚ and 339‚ each with distinct features and capabilities. The C723‚ for instance‚ is known for its versatility‚ allowing users to serve two separate soft serve flavors or a combination of both. The 794 model is renowned for its efficiency and reliability‚ making it a popular choice for busy establishments. Taylor’s 336 Soft Serve Ice Cream Machine stands out as a versatile option‚ capable of producing a variety of frozen treats‚ including ice cream‚ frozen yogurt‚ and sorbet. These models represent just a glimpse into Taylor’s extensive lineup‚ offering a solution for every ice cream dream‚ from small-scale operations to bustling food service giants.
Common Taylor Ice Cream Machine Issues
While Taylor ice cream machines are known for their reliability‚ certain issues can arise. One common problem is overload protection‚ which activates when the power supply is interrupted‚ often triggered by a power outage. Another recurring issue is inadequate mix‚ which can result from insufficient mix in the hopper. The absence of an air orifice is another potential problem‚ often due to accidental removal or improper installation. A beeping sound after a power outage is a frequent concern‚ usually stemming from the overload protection feature. Understanding these common issues enables users to diagnose and address problems efficiently‚ ensuring smooth operation and optimal performance of their Taylor ice cream machines.
Overload Protection
Taylor ice cream machines are equipped with overload protection features to safeguard the machine from damage caused by sudden power surges or outages. When the power supply is interrupted‚ the overload protection system may activate‚ triggering a beeping sound or shutting down the machine entirely. This safety mechanism prevents the motor from overheating and potentially burning out. If the overload protection system activates‚ it’s essential to check the power supply and ensure it is stable before restarting the machine. The manual provides detailed instructions on troubleshooting overload protection issues‚ including identifying and addressing potential problems with the power source or electrical components.
Inadequate Mix
One of the common issues that can arise with Taylor ice cream machines is inadequate mix. This problem occurs when there is insufficient mix in the hopper‚ preventing the machine from producing a smooth and consistent soft serve product. The manual emphasizes the importance of maintaining adequate mix levels in the hopper. It provides clear instructions on checking the mix level and adjusting it as needed. The manual also explains how to identify and address potential issues with the mix itself‚ such as improper consistency or temperature. By addressing inadequate mix issues promptly‚ you can ensure that your Taylor ice cream machine operates efficiently and consistently produces high-quality soft serve.
No Air Orifice
The Taylor ice cream machine manual highlights the importance of the air orifice‚ a crucial component that regulates the amount of air incorporated into the mix during the freezing process. This air incorporation is essential for achieving the desired texture and consistency of soft serve. The manual cautions against accidental removal or improper installation of the air orifice‚ emphasizing that it can significantly impact the quality of the final product. It explains how to properly inspect and reinstall the air orifice‚ ensuring that it is securely in place and functioning correctly. The manual also advises on how to identify and address any issues related to the air orifice‚ ensuring that your Taylor ice cream machine delivers the expected smooth and creamy soft serve.
Beeping After Power Outage
Your Taylor ice cream machine manual provides guidance on addressing a common issue⁚ the machine beeping after a power outage. The manual explains that this beeping is often a result of the machine’s overload protection feature‚ which activates during power interruptions. The manual advises checking the circuit breaker and ensuring it’s properly reset‚ as a blown fuse could also be the culprit. If the beeping persists‚ the manual suggests inspecting the mix hopper to ensure there’s an adequate amount of mix. It emphasizes the importance of checking the air orifice‚ as its absence or improper installation can contribute to the beeping. The manual also encourages contacting a local commercial equipment repair service for further troubleshooting‚ reminding you to refer to the Taylor Company Resource Library for additional support.
Taylor Ice Cream Machine Troubleshooting
Your Taylor ice cream machine manual is your guide to resolving common issues. It provides step-by-step instructions for troubleshooting various problems‚ empowering you to address them effectively. The manual begins by outlining the importance of understanding the machine’s basic functions and familiarizing yourself with its components. It then delves into specific troubleshooting techniques‚ covering a range of issues‚ from dispenser malfunctions to freezing cylinder problems. The manual emphasizes the importance of safety precautions when troubleshooting‚ especially when dealing with electrical components or potentially hazardous substances. It encourages you to consult the manual’s detailed diagrams and illustrations for visual assistance in identifying parts and understanding procedures. The manual also provides contact information for Taylor technical support‚ allowing you to seek assistance when needed.
Taylor Ice Cream Machine Manuals Online
In today’s digital age‚ accessing Taylor ice cream machine manuals online is a breeze. The Taylor Company website offers a comprehensive resource library where you can find operator’s manuals‚ service manuals‚ and other essential documentation for various models. These online manuals are readily available for download‚ allowing you to have the information you need at your fingertips‚ anytime‚ anywhere. You can search by model number or browse through a categorized list of manuals. Additionally‚ online platforms like Google and YouTube offer a wealth of resources‚ including user-generated videos and articles that provide valuable insights into operating and maintaining Taylor ice cream machines. These online resources can supplement your printed manuals‚ offering additional perspectives and tips from experienced users.
Taylor Ice Cream Machine Maintenance
Regular maintenance is crucial for ensuring the longevity and optimal performance of your Taylor ice cream machine. The Taylor Company recommends a comprehensive cleaning and inspection routine to prevent issues and maximize efficiency. Start by thoroughly cleaning the machine’s exterior‚ including the hopper‚ dispensing spout‚ and surrounding surfaces‚ using a mild detergent and warm water. Pay close attention to the freezing cylinder‚ which requires regular sanitizing with a food-grade disinfectant to eliminate bacteria and maintain product quality. Inspect the air orifice to ensure it’s free of obstructions and functioning correctly. Check the mix hopper for any signs of leaks or damage‚ and ensure the mix is fresh and properly stored. Periodically examine the machine’s electrical connections and wiring for any loose or damaged components. Regularly lubricating moving parts‚ such as the beater and dispensing mechanism‚ can prevent wear and tear. By following these maintenance guidelines‚ you can keep your Taylor ice cream machine running smoothly and producing delicious treats for years to come.
Taylor Ice Cream Machine Assembly and Sanitization
Proper assembly and sanitization are crucial for ensuring the safe and hygienic operation of your Taylor ice cream machine. Before assembling the machine‚ carefully review the instructions provided in the operator’s manual. Start by assembling the freezer base‚ ensuring all components are securely fastened. Next‚ install the freezing cylinder‚ ensuring it’s properly aligned and seated. Connect the dispensing mechanism‚ making sure it’s properly attached and functioning smoothly. Finally‚ install the mix hopper‚ ensuring it’s securely connected and ready to receive the ice cream mix. Once the machine is assembled‚ it’s essential to thoroughly sanitize all components before use. Use a food-grade disinfectant and warm water to clean all surfaces‚ including the freezing cylinder‚ dispensing spout‚ and mix hopper. Pay particular attention to crevices and hard-to-reach areas where bacteria can accumulate. Rinse all components thoroughly with clean water and allow them to air dry completely before using the machine.
Taylor Ice Cream Machine Operation
Operating a Taylor ice cream machine is a straightforward process‚ but it’s essential to follow the manufacturer’s instructions carefully for optimal performance and product quality. Before starting the machine‚ ensure the mix hopper is filled with fresh ice cream mix‚ ensuring the mix level is within the recommended range. Turn on the power switch and allow the machine to reach the desired operating temperature‚ as indicated by the control panel. Once the machine is ready‚ select the desired product settings‚ such as flavor‚ consistency‚ and dispensing speed‚ using the control panel. Begin dispensing the frozen treat‚ ensuring the flow rate is consistent and smooth. During operation‚ monitor the mix level and replenish as needed. Always maintain a clean and sanitary work environment around the machine‚ ensuring all dispensing spouts and other contact surfaces are regularly sanitized. After each use‚ thoroughly clean and sanitize the machine‚ following the manufacturer’s recommended cleaning procedures. Regular maintenance and proper operation will ensure your Taylor ice cream machine delivers consistent‚ high-quality frozen treats.
Taylor Ice Cream Machine Safety
Safety is paramount when operating a Taylor ice cream machine. Always read and understand the operator’s manual thoroughly before using the machine. Never operate the machine without proper training and supervision. Wear appropriate safety gear‚ including closed-toe shoes and gloves‚ when handling the machine. Ensure the machine is properly grounded and connected to a dedicated electrical circuit. Never overload the machine or attempt to operate it beyond its rated capacity. Exercise caution when handling hot or sharp components‚ such as the dispensing spouts and blades. Use caution when adding mix to the hopper to avoid spills or splashes. Keep children and pets away from the operating machine. Regularly inspect the machine for any signs of damage or malfunction. If you notice any issues‚ immediately stop operation and contact a qualified technician for repairs. Always adhere to local safety regulations and guidelines when operating the machine.
Taylor Ice Cream Machine Warranty
Taylor ice cream machines are backed by a comprehensive warranty that covers defects in materials and workmanship. The specific terms and conditions of the warranty may vary depending on the model and the date of purchase. The warranty typically covers parts and labor for a specific period‚ usually one year from the date of purchase. However‚ certain components‚ such as the freezing cylinder and refrigerant‚ may have a different warranty period. To ensure proper coverage‚ it is essential to register your machine with Taylor within a specified timeframe. The warranty does not cover damage caused by misuse‚ neglect‚ accidents‚ or unauthorized repairs. To file a warranty claim‚ you must contact Taylor customer service and provide proof of purchase and a description of the problem. Taylor reserves the right to deny warranty claims on machines or parts if non-Taylor-approved parts or incorrect refrigerant were installed in the machine.
Taylor Ice Cream Machine Technical Support
Taylor provides comprehensive technical support to its customers‚ ensuring that they can get the most out of their ice cream machines; If you encounter any problems with your machine‚ Taylor offers several options for assistance. You can contact their customer service team via phone or email. The team is available during business hours to answer questions‚ provide troubleshooting advice‚ and guide you through common issues. Taylor also offers online resources‚ including a library of manuals‚ FAQs‚ and troubleshooting guides‚ which can be accessed on their website. In addition‚ Taylor has a network of authorized service technicians across the country who can provide on-site repairs and maintenance. If you require assistance with your Taylor ice cream machine‚ don’t hesitate to reach out to their technical support team for expert advice and solutions.
Taylor Ice Cream Machine Parts
Taylor ice cream machines are designed for long-lasting performance‚ but like any mechanical equipment‚ parts may wear out or require replacement over time. To ensure your machine continues to operate smoothly‚ it’s essential to have access to genuine Taylor parts. Taylor offers a wide range of parts for all their models‚ including beaters‚ cylinders‚ pumps‚ hoses‚ and more. These parts are specifically engineered for Taylor machines and meet the highest quality standards. You can purchase Taylor parts directly from their authorized distributors or online retailers. When ordering parts‚ it’s crucial to provide the model number of your machine to ensure compatibility. Using genuine Taylor parts is essential for maintaining the performance‚ safety‚ and warranty of your ice cream machine.
Taylor Ice Cream Machine FAQs
Taylor ice cream machines are widely used‚ and operators often have questions about their operation‚ maintenance‚ and troubleshooting. To help address common inquiries‚ Taylor provides comprehensive resources online‚ including FAQs and support forums. These platforms offer valuable insights into frequently asked questions such as how to fix beater overload‚ cleaning frequency‚ and troubleshooting beeping issues. You can also find detailed information on specific models‚ such as the Taylor C713‚ with its two-flavor serving capabilities. Taylor’s commitment to customer support ensures that users have access to the information they need to keep their machines running smoothly and efficiently.
How to Fix Beater Overload
Beater overload is a common issue with Taylor ice cream machines‚ often caused by a buildup of frozen mix or an obstruction in the freezing cylinder. To address this‚ you’ll need to identify the source of the overload and take appropriate steps. First‚ unplug the machine and allow it to cool down. Next‚ carefully remove the beater and inspect it for any signs of damage or excessive buildup. Clean the beater thoroughly and ensure that the freezing cylinder is clear of any obstructions. If the overload persists‚ check the motor for signs of overheating or damage. If you’re unable to resolve the issue yourself‚ it’s recommended to contact a qualified technician for assistance. Remember‚ always follow the instructions in your Taylor ice cream machine manual for safe and effective troubleshooting.